Want to be in the loop?
subscribe to
our notification
Business News
LABOUR PUZZLE FOR GARMENT AND TEXTILE INDUSTRY BEFORE FOURTH INDUSTRIAL REVOLUTION
According to the Vietnam Garment and Textile Development Plan to 2020, the sector will become “one of leading export-oriented industries capable of meeting increasing domestic consumption demands and creating more jobs for society.” However, with the Fourth Industrial Revolution, garment and textile enterprises have to solve the puzzle of technological innovation and personnel rationalisation.
Opportunity from increased productivity
The garment and textile industry is an important sector with about 6,000 active enterprises and about 2.5 million workers. Most of its labour force is involved in apparel production which does not require sophisticated skills.
Despite being the largest exporter of apparels, textiles and footwear in Southeast Asia and being a top exporter of these products in the world, Vietnam's textile and garment industry still has very low labour productivity relative to other countries. It is less than a quarter of Thailand and even lower than Cambodia.
According to economists, the Fourth Industrial Revolution will provide an unprecedented opportunity to improve labour productivity. Powered by automation, robots and big data, the production capacity may increase several times. Then, employees’ incomes will improve rapidly. This is also a great opportunity for enterprises to attract skilled workers, develop more sustainably and restrict labour mobility.
Advances in digital technology such as 3D printing, programmed microcontrollers and second-generation computer-aided control have facilitated easier and cheaper high-quality customised production. Most of these trends bring good opportunities. But, they can also come with side effects with unexpected consequences that need to be managed well.
However, according to experts, technology and automation trends will accelerate rapidly in the coming time but only some countries have high levels of technology development. For developing countries like Vietnam, this process may be slower and it will be very difficult or very long for machines to completely replace humans in garment and textile production. For example, designing always requires a creative mind of human beings, not a programmed artificial intelligence.
Is the Labour force ready?
The Fourth Industrial Revolution is taking place in many fields with the advent of robotic technology and artificial intelligence with many applications in society. This is expected to have a strong impact on labour-intensive sectors like garment and textile.
With the Fourth Industrial Revolution, the workforce of the garment and textile industry will be downsized in the long term. However, in the short term, labour cost advantages still prevail and pressures on labour replacement will not be really quick and strong. Garment and textile workers are projected to scale up in the coming time.
According to forecasts on garment and textile human resources in southern Vietnam, which accounts for more than 60 per cent of garment and textile enterprises, the demand for new recruits will be 60,000 a year from 2015 to 2025, of which Ho Chi Minh City will account for 20,500 jobs. Low-skill, medium-skill and high-skill labourers will account for 50 per cent, 20 per cent and 30 per cent, respectively. These ratios show a significant decline in low-skill and medium-skill workers, while high-skill workers tend to increase. Therefore, in order to prepare well for production modernisation and catch the wave of the Fourth Industrial Revolution, worker training is extremely important.
Nevertheless, current garment and textile worker training at training facilities has yet to meet actual demand. Ho Chi Minh City, the major centre of training facilities for garment and textile workers, has 11 facilities with garment and textile training which enrol and train 1,900 students a year, including 200 at university level. The current fashion designer force in Vietnam now can assume small-scale business, not mass commercial scale.
In addition, this industry has high demand for skilled manpower in yarn, textile and dyeing sectors, estimated at 300-400 engineers a year, while universities in Vietnam can provide only about 10 per cent of this.
Therefore, in the face of opportunities and challenges in the Fourth Industrial Revolution where the pivot will be applied technology and advanced technology, Vietnam needs new innovative and appropriate ways of working to ensure development requirements and competitiveness, and one of the very first things to be done is training workers for the new context.
Source: VCCI
Related News
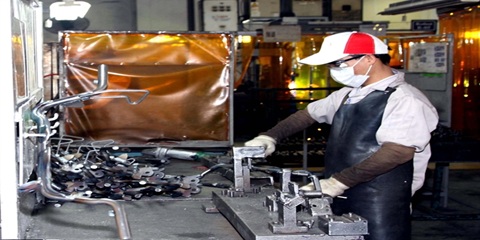
VIỆT NAM'S INDUSTRIAL PRODUCTION SEES 7.2% GROWTH IN TWO MONTHS
Việt Nam’s Index of Industrial Production (IIP) has risen by 7.2 per cent year-on-year in the first two months of 2025, according to the Ministry of Fin…
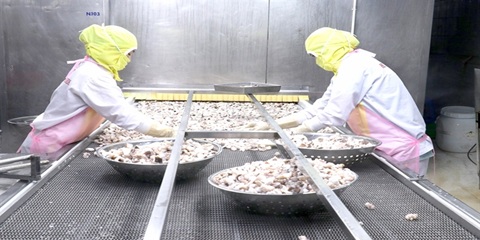
VIỆT NAM'S AGRICULTURAL EXPORTS SURGE TO FIVE-YEAR HIGH
Việt Nam’s agricultural, forestry and fishery exports hit a five-year high in the first two months of 2025, according to data released by the Mini…
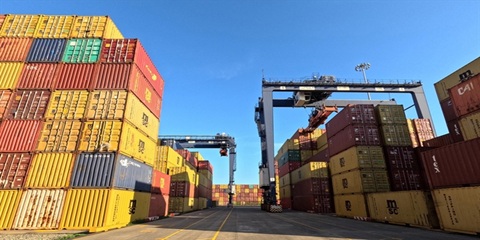
PM PUSHES FOR TRADE BALANCE AMID RISING GLOBAL COMPETITION
With a trade volume nearing $800 billion, Việt Nam ranks 23rd in terms of global exports and 22nd in imports, which represents an average a…
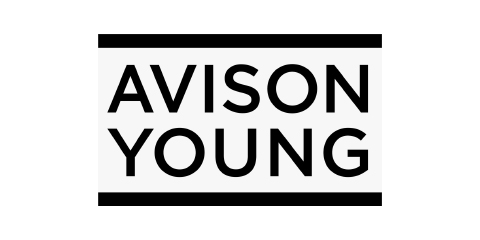
WEBINAR: KEY CONSIDERATIONS IN REAL ESTATE AND CONSTRUCTION PROJECTS
Vietnam’s property market is expanding rapidly, but legal challenges are becoming more complex. From hidden clauses in lease agreements to dis…
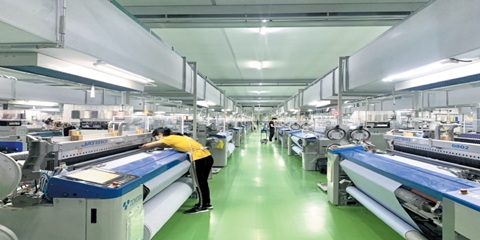
SUPPORTING INDUSTRIES KEY TO SUSTAINABLE TEXTILE-GARMENT DEVELOPMENT
In 2025, Vietnam's textile and garment industry targets US$47-48 billion in export revenue, a US$3-4 billion increase from last year. To achiev…

RUBBER INDUSTRY TO BOUNCE BACK IN 2025
Vietnam's rubber industry is poised for strong growth in 2025, driven by rising rubber prices, expanding production, and increased export op…
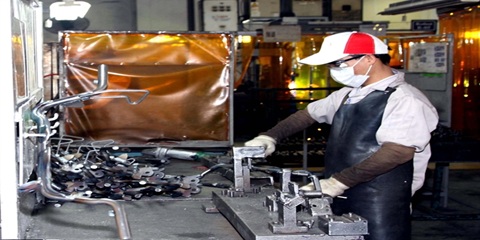
VIỆT NAM'S INDUSTRIAL PRODUCTION SEES 7.2% GROWTH IN TWO MONTHS
Việt Nam’s Index of Industrial Production (IIP) has risen by 7.2 per cent year-on-year in the first two months of 2025, according to the Ministry of Fin…
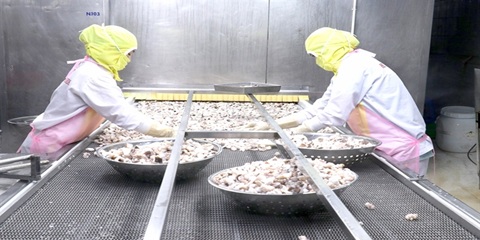
VIỆT NAM'S AGRICULTURAL EXPORTS SURGE TO FIVE-YEAR HIGH
Việt Nam’s agricultural, forestry and fishery exports hit a five-year high in the first two months of 2025, according to data released by the Mini…
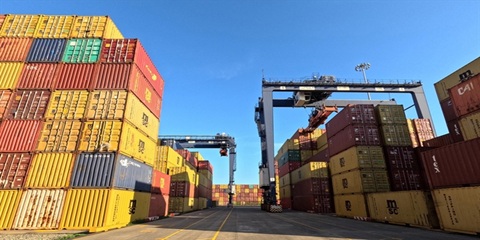
PM PUSHES FOR TRADE BALANCE AMID RISING GLOBAL COMPETITION
With a trade volume nearing $800 billion, Việt Nam ranks 23rd in terms of global exports and 22nd in imports, which represents an average a…
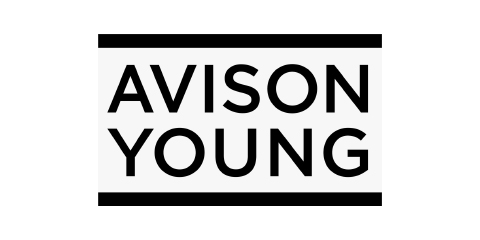
WEBINAR: KEY CONSIDERATIONS IN REAL ESTATE AND CONSTRUCTION PROJECTS
Vietnam’s property market is expanding rapidly, but legal challenges are becoming more complex. From hidden clauses in lease agreements to dis…
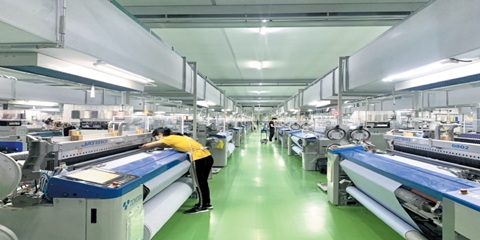
SUPPORTING INDUSTRIES KEY TO SUSTAINABLE TEXTILE-GARMENT DEVELOPMENT
In 2025, Vietnam's textile and garment industry targets US$47-48 billion in export revenue, a US$3-4 billion increase from last year. To achiev…

RUBBER INDUSTRY TO BOUNCE BACK IN 2025
Vietnam's rubber industry is poised for strong growth in 2025, driven by rising rubber prices, expanding production, and increased export op…